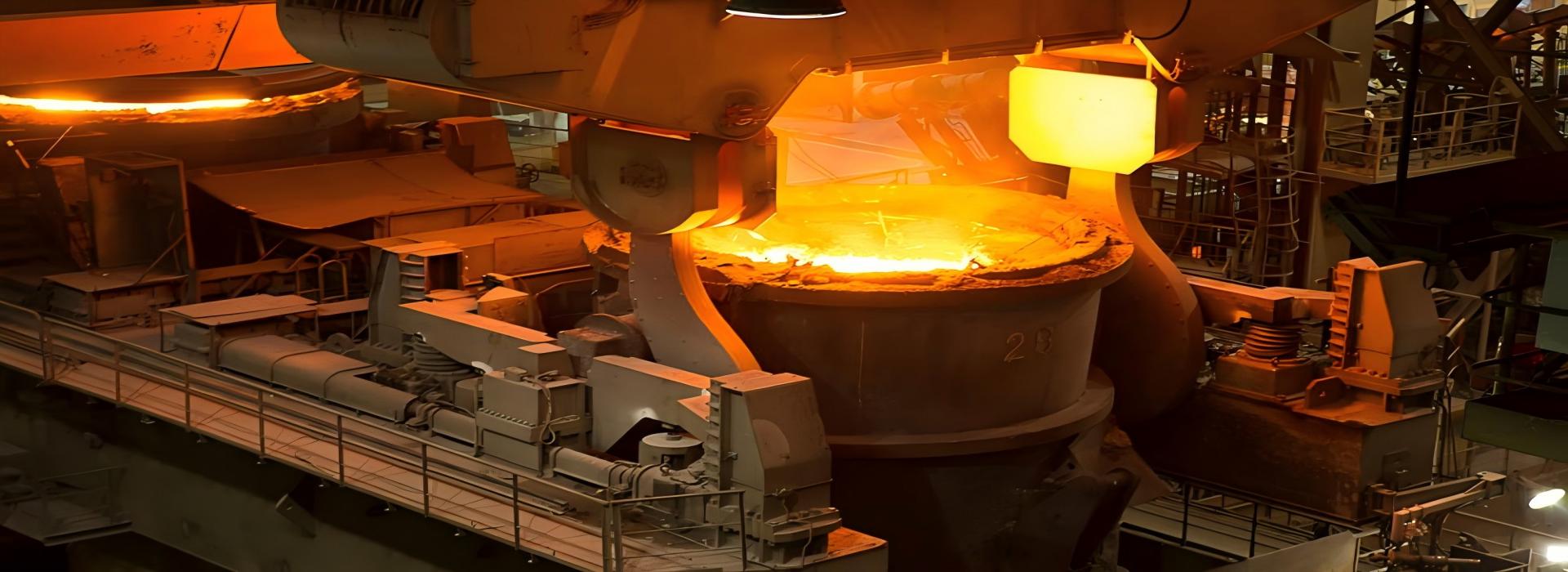
Surfacing Welding Roller
Surfacing welding roller is the key technology to repair or enhance the performance of the rollers by coating wear-resistant and high-temperature-resistant alloy materials on the surface of the rollers. The technology can significantly extend the service life of the roll, reduce equipment maintenance costs, especially for continuous casting machine in high temperature, high wear and tear in the harsh working conditions.
The main surfacing technology
1.Plasma Transfer Arc Welding(PTA)
Features: low heat input (<3 kJ/cm), dilution rate <5%, suitable for precision surfacing.
Parameters: current 80-200A, powder feed rate 30-100 g/min, layer thickness 1-3 mm.
Application: Thin-layer repair or high-precision surface strengthening.
2.Submerged Arc Welding (SAW)
Characteristics: High efficiency (deposition rate ≥15 kg/h), suitable for large-area repair.
Parameters: current 400-800A, voltage 30-40V, wire diameter 3.2-4.0 mm.
Application: Overall cladding of roll body, such as billet continuous casting roll.
3.Laser cladding
Characteristics: Dilution rate <3%, small heat-affected zone, but high equipment cost.
Parameters: Laser power 2-6 kW, scanning speed 0.5-2 m/min.
Application: Precision repair of high value rolls.
Typical application scenarios
1.Continuous casting machine fan section roll
Difficulty: Subject to casting billet belly force (up to 200 kN/m²) and thermal stress (800-1200°C).
Solution: Multi-layer surfacing with tungsten carbide + cobalt-based alloy, surface hardness ≥ HRC58.
2.Bending/straightening rolls
Difficulty: Fatigue cracks due to dynamic loading.
Solution: Nickel-based alloy transition layer + iron-based wear-resistant layer, heat fatigue cycle times up to 10⁶ times.
3.copper mold support roll
Difficulty: Cooling water corrosion and mechanical wear superimposed.
Solution: Laser cladding of Inconel 625, pitting resistance potential increased to +200 mV (SCE).
Quality control points
1.Preheat and interlayer temperature
Preheating temperature: 150-300°C (adjusted according to the carbon equivalent of the base material).
Interlayer temperature control: ≤150°C to prevent thermal cracking.
2.Non-destructive testing
Ultrasonic testing (UT): detect defects in the bonding between the cladding layer and the substrate (sensitivity Φ1 mm equivalent).
Penetration testing (PT): detect surface micro-cracks (detection accuracy 0.01 mm).
3.Residual stress management
Post-weld heat treatment: tempering at 550-600°C, holding for 2-4 hours to eliminate more than 80% of the stress.
Shot peening: surface compressive stress is raised to -400 MPa, fatigue resistance is enhanced.
Our company has many years of experience in the production and marketing of surfacing welding rollers, and we have professional and technical personnel who can produce and process according to customers’ individual needs. The above parameter data can be used for reference, if you have specific needs, please feel free to contact us.