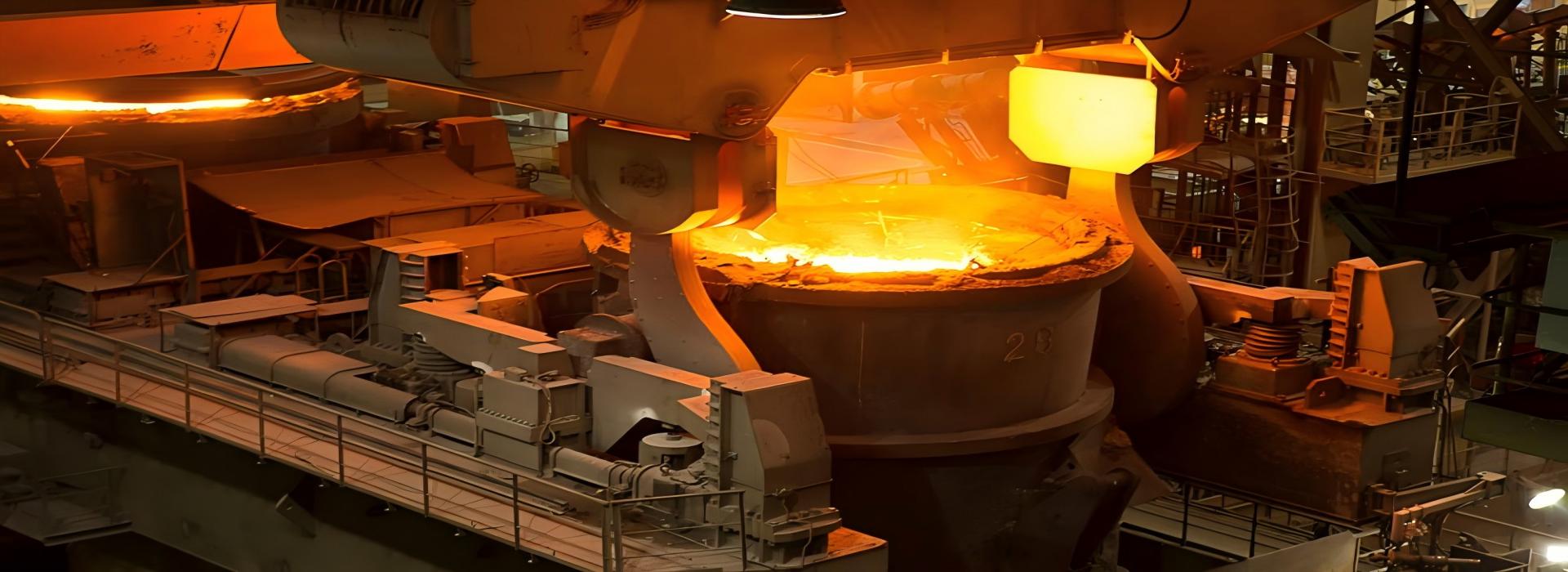
Copper Mould Tube
The copper tube is a key component in the continuous casting process, which is mainly used in continuous casting machines in the metallurgical industry. Its core role is to form a solid billet shell by rapidly cooling liquid metal (such as molten steel), thus completing the continuous casting process from liquid to solid.
1.Material Characteristics
Made of high-purity copper (such as copper, silver-copper alloy), due to its high thermal conductivity and high-temperature resistance, can quickly transfer heat.The inner wall is often plated with chrome or nickel-based alloy to enhance wear resistance, corrosion resistance, and to prevent direct contact between copper and steel resulting in adhesion.
2.Structural design
Taper design: The inner lumen of the copper tube is usually designed as an inverted cone to compensate for the shrinkage of the casting billet during solidification, reduce the air gap and enhance the cooling efficiency.
Cooling water channel: The outer wall is equipped with spiral groove or straight groove to take away heat through high-speed water flow and ensure uniform cooling.
3.Application Scenario
Mainly used in billet, billet, slab and other continuous casting process, which directly affects the surface quality and internal structure of the casting billet.
4.Common Problems and Challenges
Wear and Scratch: Friction between the billet and the inner wall of the copper tube leads to wear and tear, and the integrity of the plating needs to be checked regularly.
Thermal deformation: Deformation may occur under long term high temperature, affecting the dimensional accuracy of the billet.
Plating peeling: Plating peeling will accelerate corrosion and shorten the service life of copper tubes.
Scale clogging: Cooling water impurities are deposited in the runners, reducing cooling efficiency.
- Material and plating
High-conductivity oxygen-free copper (OFHC): purity ≥ 99.95%, thermal conductivity ≥ 380 W / (m-K), resistance to high-temperature softening, but wear resistance is poor.
Silver-copper alloy (Cu-Ag): add 0.08~0.12% silver, enhance high-temperature strength (20% increase in strength at 300℃), slightly lower thermal conductivity (about 350 W/(m-K)).
Chromium-zirconium copper (Cu-Cr-Zr): containing 0.5~1.2% Cr, 0.03~0.3% Zr, both high strength (tensile strength ≥350MPa) and thermal conductivity (320 W/(m-K)), suitable for high-draw speed continuous casting.
Inner wall chrome plating: thickness of 0.05~0.15mm, hardness ≥800HV, resistant to high temperature oxidation and steel scouring.
Inner wall nickel-based alloy plating (such as Ni-Co or Ni-Fe): thickness of 0.1~0.3mm, toughness is better than chromium plating, better resistance to thermal fatigue.
Inner wall composite plating: chromium + nickel double-layer plating, taking into account wear resistance and thermal shock resistance (high-end applications).
Nitriding treatment: Enhance the surface hardness of copper tubes to reduce initial wear.
Laser cladding: localized repair of wear areas to extend service life.
6、Reference Parameters
Square billet: common side length 100~300mm, taper 0.6~1.2%/m.
Round billet: diameter 150~400mm, taper 0.4~0.8%/m.
Slab: thickness 150~300mm, width 1000~2000mm, taper 0.8~1.5%/m.
Length: usually 700~1200mm, determined according to drawing speed and solidification time.
Single taper: simple linear taper, suitable for low drawing speed or small section billet.
Multi-taper: Segmented variable taper (e.g. double taper, parabolic taper), adapting to the complexity of solidification shrinkage and improving cooling uniformity.
Wall thickness: 8~20mm (depends on billet size and heat load).
Cooling water trough trough depth: 3~6mm, trough width: 4~8mm.
Water flow rate: 8~15m/s, water pressure: 0.6~1.2MPa.
Steel throughput: general life of 3000~10000 tons of steel (depending on the quality of plating and process conditions).
Allowable wear: inner wall plating wear ≤ 0.1mm need to be repaired, deformation more than 0.3mm need to be replaced.
Our company has rich experience in the production and marketing of crystallizer copper tubes, with professional technical personnel, according to the individual needs of customers, production and processing.The above parameter data can be used for reference, if you have specific needs, please feel free to contact us.